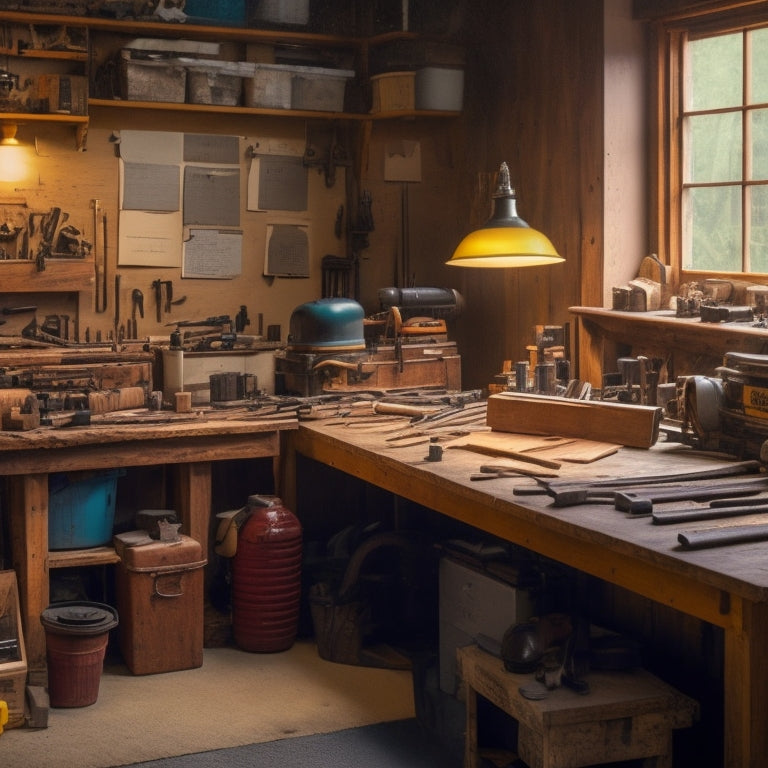
Why Woodworkers Struggle With Business Operations Management
Share
You're likely struggling with business operations management in your woodworking shop, and it's costing you time, money, and sanity. The root causes might be inefficient workshop layouts, disorganized tool and material inventory systems, or poor client communication strategies. Maybe you're juggling multiple projects without effective prioritization and time allocation, leading to missed deadlines and overwhelm. Or perhaps you're struggling with financial management, unsure of how to track expenses, manage cash flow, and plan for the future. Whatever the reason, it's clear that you need a better system in place to maximize efficiency and profitability - and you're about to discover the key to accessing it.
Key Takeaways
• Woodworkers often lack centralized systems for project management, customer information, and inventory, leading to inefficiencies and disorganization.
• Inefficient workshop layouts and poor tool organization systems hinder workflow, reduce productivity, and impact work quality.
• Insufficient time management skills, including poor prioritization and task delegation, result in missed deadlines and overwhelm.
• Disorganized tool and material inventory, and inadequate storage solutions, lead to wasted time, reduced productivity, and increased costs.
• Limited financial management knowledge and poor client communication strategies further exacerbate operational challenges and impact business profitability.
Lack of Organizational Systems
Without a centralized system to manage projects, customer information, and inventory, you're likely drowning in a sea of paperwork, scattered notes, and missed deadlines. This lack of organizational systems leads to inefficient time management, causing you to spend more hours on administrative tasks than on actual woodworking.
You struggle to keep track of customer orders, project timelines, and inventory levels, resulting in delayed deliveries, lost sales, and wasted resources. Implementing a robust project management system can help you streamline your operations and stay on top of your tasks. This system should allow you to track project progress, set reminders, and allocate resources effectively.
Additionally, an inventory control system can help you monitor your stock levels, reduce waste, and optimize your material purchasing. By automating these processes, you can free up more time to focus on what matters most – creating high-quality woodwork pieces that delight your customers.
Inefficient Workshop Layout Designs
Your workshop layout is a jumbled mess of machinery, workstations, and storage areas, hindering your workflow and causing you to waste valuable time searching for tools and maneuvering around obstacles. This inefficient workspace is a major contributor to your poor workflow, making it difficult to stay focused and productive.
You're not alone; many woodworkers struggle with optimizing their workshop layouts, leading to frustration and decreased profitability.
Take a step back and assess your current layout. Identify the 'work zones' that require the most attention, such as cutting, sanding, and assembly areas. Consider the 'work triangle' concept, where you position your most frequently used tools and machines to minimize walking distances and maximize efficiency.
Insufficient Time Management Skills
You're constantly juggling multiple projects, deadlines, and tasks, yet struggle to prioritize and allocate your time effectively, leading to missed deadlines, rushed work, and a perpetual sense of overwhelm. This is because you lack sufficient time management skills, which are vital for a woodworker's success. To overcome this, it is crucial to implement efficient time tracking and task delegation strategies.
Task | Time Allocation | Delegation |
---|---|---|
Project Planning | 30 minutes/day | Delegate to assistant |
Wood preparation | 2 hours/day | Automate with machinery |
Finishing touches | 1 hour/day | Outsource to freelancer |
Disorganized Tool and Material Inventory
Daily, wood shavings and scraps clutter your workshop, and misplaced tools hinder your productivity, as a disorganized tool and material inventory system eats away at your valuable time. You know you're not alone in this struggle. Disorganization leads to wasted time searching for tools, materials, and supplies, which ultimately affects your bottom line.
It's time to take control of your inventory. Implementing a tool maintenance schedule guarantees your equipment is in good working order, reducing downtime and increasing efficiency. Regularly inspect and maintain your tools to prevent damage and extend their lifespan.
Next, establish an inventory control system to track your materials and supplies. This helps you identify what you need to restock, reducing material procurement costs and minimizing waste. Consider investing in storage solutions like bins, shelves, and labels to keep your workshop organized and easily accessible.
Poor Client Communication Strategies
Effective workshop organization is only half the battle; now it's time to turn your attention to the client-facing side of your business, where poor communication strategies can lead to misunderstood project expectations, delayed payments, and damaged relationships. You might've a solid understanding of woodworking techniques, but without efficient communication, your client relationships will suffer.
To avoid common pitfalls, focus on these key areas:
-
Clear project scope: Guarantee you and your client are on the same page regarding project timelines, budgets, and deliverables.
-
Regular progress updates: Keep clients informed about their project's status, and be open to their feedback and concerns.
-
Defined communication channels: Establish a primary method of communication, such as email or project management software, to keep conversations organized and easily accessible.
Inadequate Project Planning and Tracking
When you take on a new woodworking project, you're likely excited to get started, but inadequate planning can quickly turn that excitement into frustration. You may find yourself struggling to meet unrealistic timeline expectations, allocating resources inaccurately, or mismanaging task priorities - all of which can lead to costly mistakes and delays.
Unrealistic Timeline Expectations
You often underestimate the time it takes to complete a woodworking project, leading to unrealistic timeline expectations that can derail your entire production schedule. This happens when you fail to account for the intricacies of each project, resulting in rushed deadlines that are impossible to meet.
As a result, you're left dealing with frustrated clients, delayed shipments, and a damaged reputation.
To avoid this, developing a more realistic understanding of the time required for each project is crucial.
Here are three key factors to keep in mind:
-
Task segmentation: Break down complex projects into smaller, manageable tasks to get a more precise estimate of the time required.
-
Material lead times: Factor in the time it takes to source and receive materials, as well as any potential delays.
-
Contingency planning: Incorporate buffers for unexpected setbacks, such as equipment failures or last-minute design changes.
Inaccurate Resource Allocation
Two major pitfalls in woodworking business operations management are inadequate project planning and tracking, which lead to inaccurate resource allocation, causing projects to spiral out of control.
When you fail to plan and track your projects effectively, you'll likely mismanage your resources, allocating too much time to one task and not enough to another. This can lead to delays, cost overruns, and a significant decrease in profit margins.
You might find yourself spending too much time on a single task, only to realize you've gone way over budget. Inaccurate budgeting and project scheduling can also lead to resource mismanagement, as you'll struggle to allocate your materials, tools, and labor efficiently.
To avoid this, you need to develop a detailed project plan, breaking down each task into manageable chunks and allocating specific time frames for each. By doing so, you'll be able to track your progress, identify potential bottlenecks, and make adjustments as needed.
Mismanaged Task Priorities
Without a clear project plan, tasks can quickly spiral out of control, and mismanaged task priorities can lead to wasted time, energy, and resources. As a woodworker, you know how essential it's to manage your tasks efficiently to meet deadlines and deliver quality work.
However, when you're not clear on what needs to be done, and when, it's easy to get bogged down in non-essential tasks.
To avoid this, you need to prioritize your tasks effectively. Here are three ways to do so:
-
Identify critical tasks: Determine which tasks are essential to completing your project on time. Focus on these tasks first, and delegate or defer less critical tasks accordingly.
-
Use time-blocking: Schedule specific times for each task, ensuring you're allocating sufficient time for each activity. This helps you stay focused and avoid multitasking, which can decrease productivity.
-
Set realistic deadlines: Establish realistic deadlines for each task, considering your workload, resources, and potential roadblocks. This helps you avoid overcommitting and reduces stress.
Limited Financial Management Knowledge
Many woodworkers struggle to manage their business's financial operations effectively because they lack a solid understanding of financial management principles and practices. This limited knowledge can lead to poor financial planning, which is critical to the success of your woodworking business. You may find yourself constantly worrying about cash flow, profitability, and meeting financial obligations.
Here's a breakdown of what you should be doing:
Financial Aspect | Your Current Reality |
---|---|
Financial Planning | You're not creating a detailed plan, leaving you uncertain about your financial future. |
Budget Tracking | You're not accurately tracking expenses, making it difficult to identify areas for cost reduction. |
Cash Flow Management | You're struggling to manage cash inflows and outflows, leading to financial stress. |
Unproductive Workshop Habits and Routines
You know that every minute counts in your workshop, but do you realize how much time you're wasting searching for misplaced tools or moving through a cluttered workspace?
Your current habits and routines might be holding you back from achieving maximum productivity.
Take a closer look at your workshop's layout and tool organization systems – you might be surprised at how a few simple changes can add up to significant time savings.
Cluttered Workspace Wastes Time
Across your workshop, scattered tools and materials are slowing you down, turning what should be a well-oiled machine into a frustrating game of hide-and-seek. Every minute spent searching for misplaced items is a minute taken away from actual woodworking. It's time to take control of your workspace and boost your productivity.
Here are three areas to focus on to improve your workspace efficiency and time management:
-
Designate a home for each tool: Assign a specific spot for each tool and material, making it easy to find what you need when you need it.
-
Implement a 'one-touch' rule: Try to put things away in their designated spot as soon as you're done using them, avoiding clutter buildup.
-
Schedule regular cleaning sessions: Set aside time each week to tidy up your workshop, ensuring everything remains organized and within reach.
Inefficient Tool Organization Systems
Your well-organized workspace is only as strong as its weakest link, and for many woodworkers, that link is an inefficient tool organization system that's holding them back from maximum productivity.
You might've a tidy workspace, but if your tools are scattered all over the place, you're wasting precious time searching for them. Inefficient tool organization also leads to poor tool maintenance, which can reduce the lifespan of your tools and affect the quality of your work.
To optimize your workshop efficiency, you need a well-thought-out tool storage and maintenance system. This means designating a specific space for each tool, using storage solutions like pegboards, cabinets, and bins, and establishing a regular maintenance routine.
A well-organized tool system allows you to quickly find the tool you need, reduces downtime, and increases your overall productivity. By streamlining your tool organization, you'll be able to focus on what matters most – creating high-quality woodworking pieces that showcase your skills.
Frequently Asked Questions
How Do I Prioritize Tasks When Faced With Multiple Project Deadlines?
You prioritize tasks by identifying critical deadlines, breaking projects into manageable chunks, and allocating time for each task based on its urgency and importance, ensuring effective workload management and timely delivery.
What Software Is Best for Managing Client Relationships and Projects?
You'll find that CRM software like HubSpot or Zoho CRM helps you manage client relationships and projects efficiently, offering task management and project tracking features to streamline your workflow and guarantee timely communication.
Can I Outsource Business Operations Tasks to Free up Workshop Time?
"You're the master chef in your workshop kitchen, but bogged down by admin tasks. Consider outsourcing time-consuming operations to free up hours, much like delegating prep work to a sous chef, and watch your workshop efficiency sizzle!"
How Often Should I Review and Adjust My Business Operations Strategy?
You should regularly review your business operations strategy, ideally quarterly, to evaluate its effectiveness and implement adjustments, refining your approach to guarantee it aligns with your goals and stays on track.
What Metrics Should I Track to Measure Business Operations Success?
You know that 80% of businesses fail to achieve their goals due to poor performance analysis. To measure business operations success, you should track key performance indicators like production capacity, lead time, and efficiency measurement, visualizing data to identify areas for improvement.
Related Posts
-
7 Essential Foldable Workbenches for Garages
When selecting a foldable workbench for your garage, you'll want to contemplate factors such as space-saving design, ...
-
Tool Storage Chests for a More Organized Workspace
You're looking to enhance productivity and reduce stress in your workspace by getting your tools organized, and that'...
-
Top 7 Parts Tray Organizers for Productivity
You can optimize your workspace and enhance productivity with the right parts tray organizer, which can help you cate...