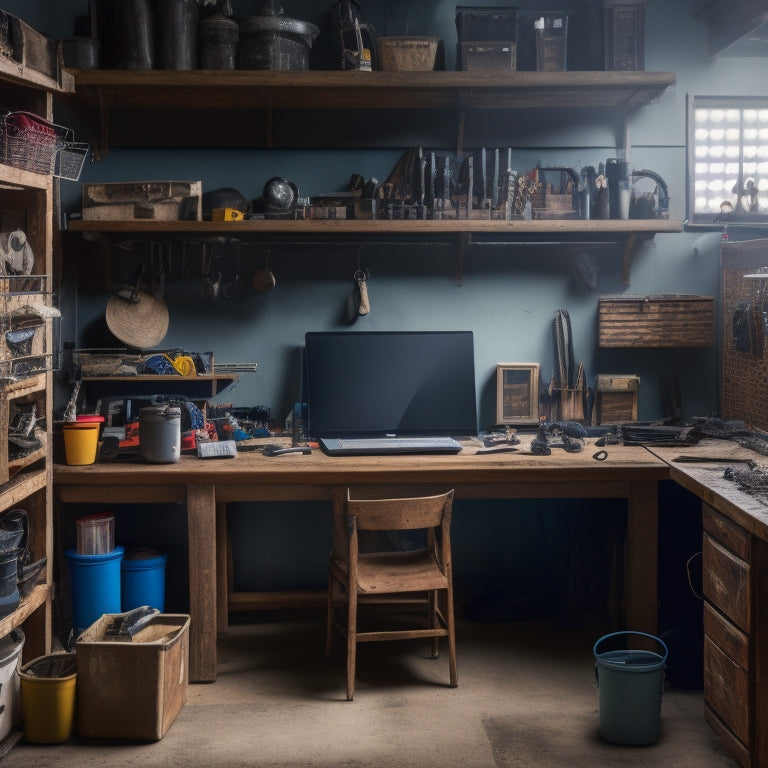
Create a DIY Tool Inventory Management System
Share
To create a DIY tool inventory management system, start by gathering all your tools in a well-lit space to assess their quality and identify duplicates or worn-out items. Categorize tools into broad and subcategories based on function, and group them by functionality, storage needs, and frequency of use. Create a centralized tool database to track tool details, condition, and maintenance records. Designate a specific storage area, label tools clearly, and consider color-coding categories for easy navigation. Establish a routine for inspecting tools and recording their condition. By following these steps, you'll be well on your way to optimizing your tool collection and uncovering ways to boost productivity and save time.
Key Takeaways
• Assess your tool collection to identify duplicates, worn-out items, and determine which tools to keep, donate, sell, or discard.
• Categorize and group tools by function, storage needs, and frequency of use to prioritize and track them efficiently.
• Create a centralized tool database to track tool details, performance, and maintenance, and make informed purchasing decisions.
• Designate a specific storage area and implement a labeling system to keep tools organized, easily accessible, and prevent clutter.
• Establish a routine for inspecting tools, recording their condition, and scheduling maintenance to prevent equipment failure and ensure timely repairs.
Assessing Your Tool Collection
Take stock of your entire tool collection by gathering every tool from your workshop, garage, or storage areas and laying them out in a well-lit, open space. This will give you a clear view of what you have, making it easier to evaluate tool quality and identify any duplicates or items that need replacement.
As you examine each tool, ask yourself if it's still in good condition, if it's still useful, or if it's time to let it go. Consider the tool's age, usage, and performance. Are there any signs of wear and tear? Does it still function as intended? Be honest with yourself, and set aside any tools that are no longer serving you well.
This process will help you decide what to keep, what to donate or sell, and what to discard. Once you've purged your collection, you can start thinking about organizing tool storage. You'll want to create a system that keeps your tools easily accessible, protects them from damage, and makes the most of your available space.
Categorizing and Grouping Tools
Now that you've taken stock of your tools, it's time to organize them in a way that makes sense.
You'll want to create a system that categorizes tools by type, function, or frequency of use, and groups them in a way that streamlines your workflow.
Tool Classification System
You'll need a clear tool classification system to categorize and group your tools in a way that makes sense for your specific DIY projects and workshop setup. A well-organized system will help you locate tools quickly, optimize tool organization, and streamline storage solutions.
Start by categorizing tools into broad groups, such as hand tools, power tools, and specialty tools. Then, create subcategories within each group based on the tool's function, like 'measuring' or 'cutting'. This will help you identify patterns and relationships between tools, making it easier to find what you need when you need it.
When creating your classification system, consider factors like tool maintenance and repair techniques. For instance, you may want to group tools that require similar maintenance tasks, like lubrication or sharpening, together. This will save you time and effort in the long run.
Tool Grouping Methods
Tool Grouping Methods
With your tool classification system in place, categorize your tools into groups based on their functionality, storage needs, and frequency of use to optimize your workshop's layout and workflow. This will enable you to create a more organized and efficient tool organization system.
Here's an example of how you can group your tools:
Tool Group | Description | Example Tools |
---|---|---|
Fasteners | Tools used for fastening and joining materials | Hammers, screwdrivers, wrenches |
Cutting | Tools used for cutting and shaping materials | Saws, knives, drill presses |
Measuring | Tools used for measuring and testing materials | Tape measures, levels, multimeters |
Prioritizing Essential Tools
Categorize your essential tools by labeling them as 'must-haves,' 'nice-to-haves,' or 'luxury items' to distinguish between the tools you use daily and those that are only occasionally necessary. This prioritization will help you focus on tool maintenance and organization.
For instance, your must-haves might include a hammer, tape measure, and level, which you use frequently.
Nice-to-haves could be a circular saw or drill press, which are useful but not essential for everyday tasks.
Luxury items might include specialized tools like a router or jigsaw, which are nice to have but not necessary for most projects.
Creating a Tool Database
By establishing a centralized tool database, you'll be able to efficiently track and manage your DIY tool collection. This database will serve as the backbone of your inventory organization, allowing you to keep tabs on every tool, accessory, and supply.
To create your database, start by deciding on a format that works for you, such as a spreadsheet, notebook, or app. Next, categorize your tools by type, frequency of use, or project application. This will make it easier to locate specific tools when you need them.
When adding tools to your database, be sure to include essential details like the tool's name, description, location, and condition. You may also want to track the purchase date, cost, and warranty information. By doing so, you'll be able to monitor tool performance, identify areas for improvement, and make informed purchasing decisions.
Effective tool tracking will save you time, reduce frustration, and help you provide better service to those you're serving. With a well-organized database, you'll be able to quickly locate the tools you need, ensuring that your projects are completed efficiently and effectively.
Setting Up a Storage System
Your DIY tool collection deserves a storage system that's just as organized as your database, so start by designating a specific area or constructing a dedicated storage unit that can accommodate your tools and accessories. This will help you keep everything in one place, making it easier to find what you need when you need it.
When setting up your storage system, consider an organizing layout that groups similar tools together, such as all your power tools in one section and hand tools in another. This will help you quickly locate specific tools and prevent clutter from accumulating.
A labeling system is also essential to make sure you can easily identify what's stored in each bin or on each shelf. Use clear labels that indicate the contents, and consider color-coding categories to make it even easier to navigate.
Tracking Tool Condition and Maintenance
You'll want to establish a routine for regularly inspecting your tools and recording their condition to guarantee they remain in good working order. This will help you identify potential issues before they become major problems, saving you time and money in the long run.
Set up a tool maintenance tracking system to log the condition of each tool, including any repairs or maintenance performed. This can be as simple as a spreadsheet or a notebook dedicated to tool maintenance tracking.
Organize your inventory by categorizing tools by type, frequency of use, or location. This will make it easier to identify which tools need more frequent inspections or maintenance.
Create a tool maintenance schedule to make sure regular check-ups and prevent equipment failure. For example, schedule monthly inspections for frequently used tools and quarterly inspections for less frequently used ones.
Implementing a Loaner System
To reduce tool downtime and minimize delays, consider implementing a loaner system that allows you to temporarily replace a tool with a spare or rental unit while the primary tool is being repaired or maintained. This system guarantees that your team can continue working efficiently, even when a tool is unavailable.
To make the loaner system effective, you'll need to establish borrowing policies and loaner agreements. This includes determining who is authorized to borrow loaner tools, how long they can keep them, and what the consequences are for not returning them on time.
Here's a sample loaner tracking system to help you get started:
Loaner Tool | Tool Availability |
---|---|
Drill | Available |
Circular Saw | Out for repair |
Impact Driver | Rented from supplier |
Wrench Set | Loaned to John Smith until 02/15 |
Frequently Asked Questions
Can I Use a Physical Notebook for My Tool Inventory Management?
You can use a physical notebook for tool inventory management, but it'll be time-consuming and prone to errors. Consider digital solutions like Excel spreadsheets for ease of tracking, or even barcode scanning and RFID tracking for a more efficient system.
How Do I Handle Tools That Serve Multiple Purposes or Functions?
"Coincidentally, you're not alone in struggling with multi-functional tools! When organizing, categorize them by primary function, then prioritize utility by secondary uses, ensuring you're maximizing their potential without duplicating efforts in your inventory management."
What if I Have Tools That Are Difficult to Categorize?
When faced with tools that defy categorization, you'll find that creating custom labels and utilizing visual organization methods, like color-coding or icons, can help you effectively identify and store these unique items in your inventory system.
Can I Use a Tool Inventory Management App for Personal Use?
"Did you know 75% of small businesses use mobile apps to streamline operations? You can definitely use a tool inventory management app for personal use, choosing from various mobile app options that cater to both personal and professional needs."
How Often Should I Update My Tool Inventory Management System?
You'll want to update your tool inventory management system regularly, ideally weekly or bi-weekly, to guarantee accuracy and efficiency, which will lead to cost savings and improved productivity.
Related Posts
-
Open Storage Bins for Shelving Units
You need open storage bins that integrate seamlessly with your shelving units to boost your organization, productivit...
-
Essential Steps for Garage Storage System Design
You're about to change your cluttered garage into an organized haven by following a structured approach to garage sto...
-
Must-Try Bike Storage Ideas in Small Spaces
You're tired of sacrificing precious living space to store your bike, especially in small homes where every square fo...